The Partner That Never Takes a Day Off: Continuous Improvement
- Nina Keyrouz
- Feb 25
- 5 min read
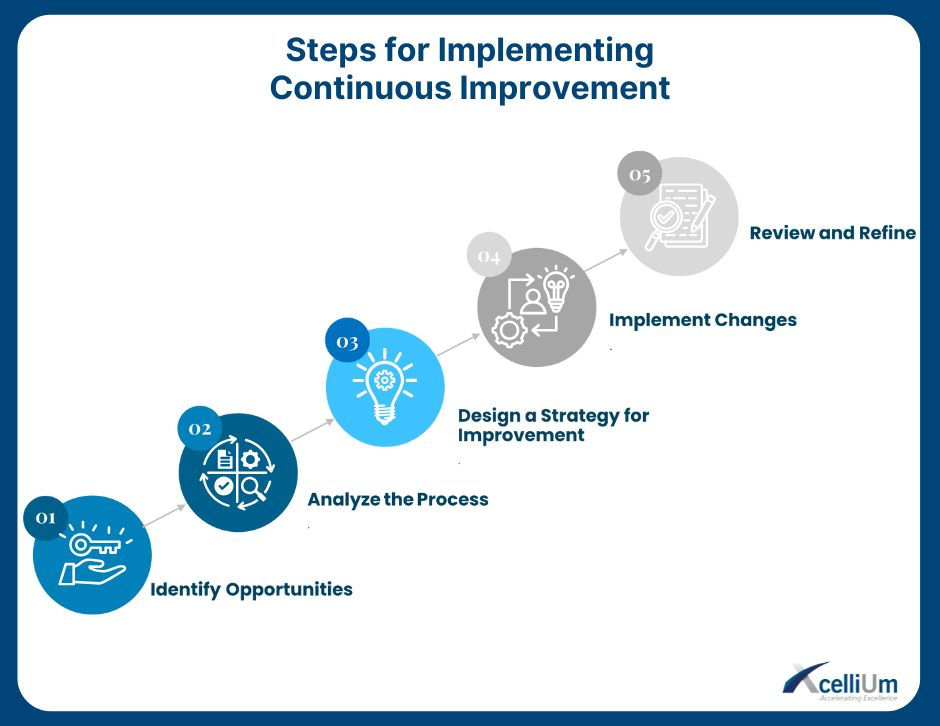
Imagine walking into a workplace where everything just flows—processes run smoothly, employees proactively solve problems, and small improvements happen every day. No chaos, no firefighting, just steady progress. Sounds ideal, right? Well, this isn’t just a dream; it’s what happens when organizations embrace continuous improvement.
Some companies turn to continuous improvement when they’re in crisis, using it as a tool to turn things around. But here’s the real game-changer: 62% of companies adopt continuous improvement not just to fix problems, but to move from good to great.
So, what makes continuous improvement so powerful? And how can businesses integrate it into their strategy for long-term success? Let’s dive in!
“Improvement means the elimination of waste, and the most essential precondition for improvement is the proper pursuit of goals. We must not be mistaken, first of all, about what improvement means. The four goals of improvement must be to make things easier, better, faster, and cheaper.” - Dr. Shigeo Shingo
Continuous Improvement: Small Steps, Big Results
Continuous improvement is more than just a strategy; it’s a philosophy that integrates deeply into an organization’s culture. It is rooted in the principle of Kaizen, which translates to “change for the better” or “continuous improvement.” The core of this philosophy is the belief that there is always room for improvement in every aspect of an organization’s operation, no matter how small. This approach contrasts starkly with the mindset of making occasional, radical changes.
One of the key strengths of continuous improvement is its emphasis on ongoing, minor modifications. These small changes are less disruptive and more manageable than large-scale reforms, making them more accepted by the workforce and easier to implement. Over time, these incremental changes add up, resulting in significant overall improvement.
Guiding Principles for Continuous Improvement: Lessons from Shingo Prize Winners
Dr. Shigeo Shingo, the visionary behind the Shingo Model, laid the foundation for a transformative approach to Continuous Improvement. His guiding principles serve as a roadmap for organizations striving for operational excellence, fostering a culture of learning, innovation, and efficiency. These principles emphasize the importance of mindset, scientific thinking, process optimization, and quality assurance—key elements that drive sustainable improvement and long-term success.
Seek Perfection: Perfection is an aspiration that may never be fully attained, yet the pursuit of it fosters a culture of continuous improvement. The only true limitations are the paradigms through which we perceive and understand our organization’s current reality.
Lessons Learned: In 2024, Ipsen Manufacturing Ireland Ltd. received the Shingo Prize for operational excellence. The Dublin site, with nearly 200 employees, produces active pharmaceutical ingredients and has fostered a culture where every colleague understands how their work supports the company's strategy, focusing on continuous improvement and alignment between values and behaviors.
Embrace Scientific Thinking: Innovation and improvement stem from repeated cycles of experimentation, direct observation, and learning. A systematic and relentless exploration of new ideas, including failures, refines our understanding of reality and fuels continuous progress.
Lessons Learned: In 2023, Jabil Circuit Shanghai Ltd. was awarded the Shingo Prize. The organization implemented systematic problem-solving methodologies, encouraging teams to experiment, observe outcomes, and learn from failures, leading to innovative solutions in their processes.
Focus on Process: All outcomes are a direct result of the processes that create them. Even the most capable individuals cannot consistently deliver ideal results if they are working within flawed processes. Instead of attributing failures to people, organizations must identify and refine underlying process inefficiencies.
Lessons Learned: In 2023, Abbott Logistics Breda in the Netherlands received the Shingo Prize. The company emphasized process optimization, ensuring that each step in their operations was efficient and effective, leading to high-quality outcomes.
Assure Quality at the Source: Achieving perfect quality requires ensuring that every task is completed correctly the first time. Any defect or error in a product or service must be detected and addressed immediately at the point of creation to prevent its escalation.
Lessons Learned: In 2024, Baxter's Hillrom SAS facility in Pluvigner, France, was honored with the Shingo Prize. They implemented rigorous quality assurance practices, empowering employees to identify and rectify defects immediately, ensuring high standards in their products.
Improve Flow & Pull: The highest value for customers is delivered when products and services are created in response to actual demand and flow seamlessly through the system. Disruptions in this flow introduce waste, making it essential to minimize inefficiencies and optimize responsiveness.
Lessons Learned: In 2023, BHP Escondida Cathodes in Antofagasta, Chile, received the Shingo Prize. The organization optimized its production processes to respond effectively to customer demand, ensuring a smooth and efficient flow of products through its system.
Implementing Continuous Improvement: Steps to Ensure Success
By stabilizing processes, establishing standard work, observing directly, focusing on value streams, simplifying and visualizing processes, eliminating waste, and ensuring no defects are passed forward, organizations can build a solid foundation for continuous improvement. These steps create a cycle of improvement that leads to greater efficiency, higher quality, and sustained long-term success.
Implementing continuous improvement in an organization involves several key steps. As a culture and excellence expert with experience in food processing, manufacturing, and …., I’ve seen firsthand how effective the following steps can be in driving significant improvements.
Step 1: Identify Opportunities
The first step in the continuous improvement process is identifying areas for enhancement. This involves assessing current processes—often referred to as the ‘as-is’ state—to pinpoint inefficiencies and performance gaps. In industries like food processing, for example, this could mean reducing waste, optimizing production lines, or improving product quality.
Effective techniques for uncovering opportunities include employee feedback sessions, customer surveys, and performance data analysis. One recommended approach is conducting a waste walk—observing workflows directly on the shop floor to identify inefficiencies. Lean tools like 5S can help streamline these processes by eliminating wasteful activities.
Step 2: Analyze the Process
Once improvement areas are identified, the next step is to analyze the processes in detail. The goal is to understand the root causes of inefficiencies rather than just addressing symptoms. In manufacturing, tools like value stream mapping provide a visual representation of workflows, helping identify bottlenecks and areas of waste. A thorough analysis ensures that any changes made are data-driven, targeted, and effective.
Step 3: Design a Strategy for Improvement
After analysis, the focus shifts to designing a strategy for improvement. This involves defining specific changes, determining required resources, and aligning initiatives with the organization’s strategic goals. For example, in the automotive industry, introducing automation in specific areas can enhance efficiency. A well-structured plan should outline clear objectives, timelines, and measurable outcomes to ensure a smooth transition from planning to execution.
Step 4: Implement Changes
This is the action phase, where the planned improvements are put into practice. Clear communication with all stakeholders is critical to ensure alignment and smooth execution. Training and support may be necessary to help employees adapt to new processes. Monitoring progress in real-time allows for quick adjustments if challenges arise. Even the most well-planned strategy can fail without proper execution, making this step vital to success.
Step 5: Review and Refine
The final step is to assess the effectiveness of the implemented changes. Data collection, performance analysis, and comparison against initial objectives help determine whether the improvements have delivered the expected results. Continuous feedback loops ensure that the changes are sustainable and adaptable over time.
Organizations that embed continuous improvement into their culture don’t just achieve incremental gains - they foster long-term agility, resilience, and excellence.The question is, how ready is your organization to take the next step? With the right mindset, strategy, and tools, continuous improvement isn’t just a goal—it’s a journey toward sustained success.
Nina Keyrouz
Learning & Development Expert

Comments